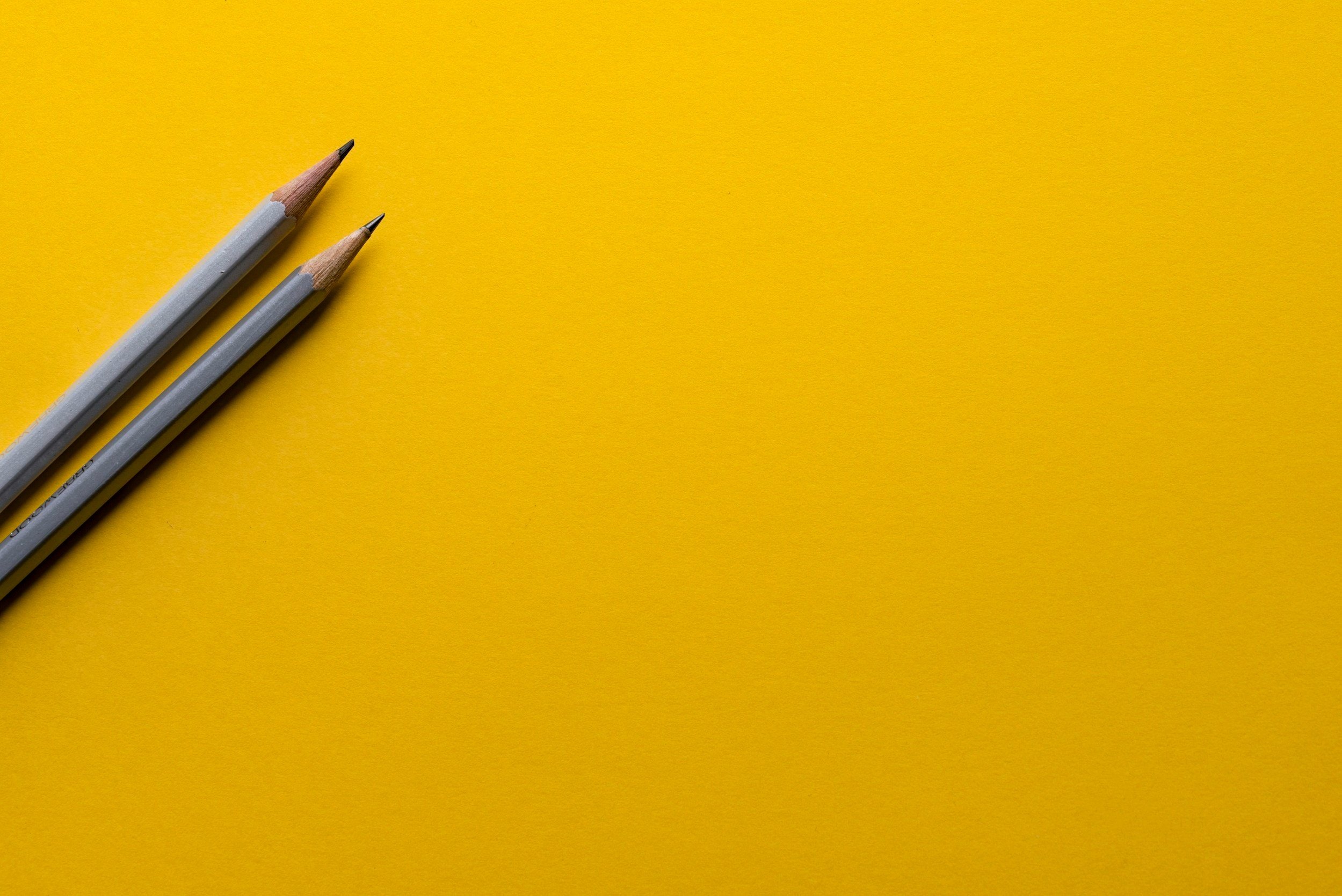
Gantry Inspection
OSHA Crane Inspection Requirements
OSHA outlines many of the specific terms they use in their crane inspections in OSHA 1910.179, including the difference between overhead cranes and gantry cranes. It’s a good idea to study those terms so you can be sure you understand all the crane regulations that apply to you and your business.
Beyond those specific terms, OSHA 1910.179 has various regulation requirements listed for different situations involving cranes. We’ll touch on a few of the most important and most asked-about regulations below:
Annual inspection: OSHA requires an annual inspection of cranes, but there has been some question in the past about what constitutes an annual inspection. To put it simply, if you have a crane inspected on June 1, it needs to be inspected on or before June 1 of the following year. Doing so will fulfill the timeframe for an annual OSHA inspection.
Competent person: According to OSHA, a competent person must perform all crane inspections. A competent person is essentially a qualified person who you will appoint to carry out the crane inspection, inspecting all machinery and equipment before and during use.
Out-of-country inspections: If a competent person performs a crane inspection in another country, OSHA will accept the inspection results and allow operation of the crane within United States borders. This is because OSHA does not specify where the inspection is to take place in their regulations.
Types of inspections: There are four main types of crane inspections that OSHA specifies. These are initial inspections, functional test inspections, frequent inspections, and periodic inspections. You can learn more about these in the sections below.
Initial Inspection
According to OSHA, the first inspection classification is your initial crane inspection, which requires a qualified person to inspect all new and altered cranes prior to initial use. For the safety and efficiency of your workers and workplace, it’s important to determine that new or newly modified lifting equipment is in safe working order before it’s put into service. To complete a thorough initial crane inspection, one must closely inspect the following:
Hoisting and lowering: Hoist motion is defined by OSHA as the motion of a crane that raises and lowers a load.
Trolley and bridge travel: Bridge and trolley travel controls must be located where the operator can readily face the direction of travel
Limit switches, locking, and safety devices: The trip setting of hoist limit switches must be determined using an empty hook traveling at increasing speeds until it reaches the maximum. The actuating mechanism of the limit switch must be located to trip the switch under all conditions and with sufficient time to prevent contact of the hook or hook block with any part of the trolley.
Rated load test: Test loads should not be more than 125 percent of the rated load, and test reports should be placed on file and readily available to appointed personnel.
This initial inspection also applies to reinstalled and repaired cranes. However, inspections of repaired and modified cranes may be limited to the provisions affected by the actual alteration, repair, or modification. This distinction should be determined by a qualified person. All inspection reports for initial use should be dated, signed, and kept on file should they be needed at a later date.
Functional Test Inspection
The functional test inspection is a daily inspection of all functional operating mechanisms to check for any inconsistencies that interfere with proper crane operation. A competent person should perform this inspection before every shift and should use their visual knowledge of cranes to check for the following:
Leakage or deterioration in lines, valves, tanks, drain pumps, and other parts of the crane’s hydraulic or air systems
Excessive wear, twist, stretching, or distortion on hoist chains
Cracks and deformation on hooks
Excessive wear of components of all functional operating mechanisms
Noncompliance with manufacturer recommendations for rope reeving
These inspections include observation during operation. Crane operators should look for any defects that might appear between regular inspections. All deficiencies should be carefully examined and a determination made as to whether or not they constitute a safety hazard.
Frequent Inspection
According to OSHA, operators or other designated personnel should visually inspect their overhead cranes at frequent intervals to maintain their proper use.
For monthly frequent inspections, the designated person should complete a certification record that includes the date of the inspection, the signature of the person who performed the inspection, and an identifier of the part that was inspected. During monthly frequent inspections, operators and other designed workers should carefully examine the following items as part of their inspection guidelines:
Monthly: Hooks with deformation or cracks—written record with signature of inspector and date
Monthly: Hoist chains and end connections for wear, twist or distortion (written record with signature of inspector and date)
Monthly: Running Rope and end connections for wear, broken strands, etc. (written record with signature of inspector, rope identity, and date)
As needed: Functional operating mechanisms for excessive wear
As recommended: Rope reeving according to manufacturers’ recommendations
Periodic Inspection
According to OSHA, periodic inspections should occur at different intervals depending on the crane’s service type. For example, a crane that performs infrequent, light, or normal service should be fully inspected annually. A heavy service crane should be fully inspected semiannually to annually, depending on the nature of the crane’s critical components and the degree of their exposure to wear or deterioration. A severe service crane should be fully inspected monthly to quarterly.
These periodic inspections require a complete inspection of the overhead crane by a qualified inspector. Any deficiencies must be carefully examined and a determination must be made as to whether or not they constitute a safety hazard. Period inspections should (at the very least) include:
Deformed, cracked, or corroded members
Loose bolts or rivets
Cracked or worn sheaves and drums
Worn, cracked, or distorted parts (pins, bearings, gears, rollers, etc.)
Excessive wear on brake-system parts
Inaccuracies in load, wind, and other indicators
Electric of fossil fuel motors
Excessive wear of chain drive sprockets and chain
Deteriorated electrical components (pushbuttons, limit switches, or contactors)
Upon completion of periodic inspections, the qualified inspector should examine deficiencies and determine whether they constitute a safety hazard. If so, the qualified inspector must then decide whether the crane should be removed from service until it’s been repaired. When in doubt, remove the crane from service. Once the inspector has completed the full inspection, he or she must date and sign the inspection record. The inspection records should be kept on file and readily available should the need arise.